Acero verde, el material que el mundo necesita para seguir creciendo
El acero ha sido y es una de las piezas esenciales para la evolución económica y social de los últimos siglos. El desafío ahora es producirlo sin usar combustibles fósiles y con tecnologías respetuosas con el medioambiente. Por ahora, el acero verde pasa por emplear hidrógeno en el proceso de producción.
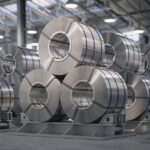
En los cimientos de los edificios, en los electrodomésticos, en los coches y bicicletas y hasta en los cubiertos de la cocina. Basta con echar un vistazo a nuestro alrededor para confirmar que el acero es una de las bases sobre las que se construye el mundo que nos rodea y uno de los materiales más usados en todo el planeta.
El acero es, también, una de las piezas que ha permitido el desarrollo económico y social de los últimos siglos. Y, ahora, el sector siderúrgico se enfrenta a un desafío: transformar los sistemas de producción para conseguir el codiciado acero verde, más sostenible y responsable con el medioambiente.
Se calcula que la producción de acero se ha multiplicado por diez desde 1950, y algunas estimaciones señalan que la demanda podría doblarse en las próximas tres décadas. Por ello, lograr el cambio estructural y tecnológico que haga realidad el acero verde es cada vez más urgente.
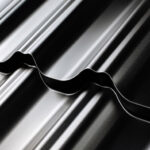
¿Qué es el acero verde?
El acero verde es aquel que se produce sin que entren en juego los combustibles fósiles, y que resulta sostenible teniendo en cuenta toda su vida útil, desde su producción hasta su uso y posterior reciclado o reutilización.
“Es un acero convencional en cuanto a composición y prioridades, pero con cero emisiones de carbono durante su producción”, explica Juan José de Damborenea, profesor de Investigación en el Centro nacional de Investigaciones Metalúrgicas (CNIM-CSIC) y actual presidente de la Sociedad Española de Materiales (SOCIEMAT). “Desde el punto de vista de las propiedades, tanto de su resistencia mecánica como de su durabilidad y versatilidad, no hay diferencias entre el acero verde y el convencional. Se trata, en definitiva, de la misma aleación, pero fabricado con una tecnología respetuosa con el medioambiente”, añade De Damborenea.
Tal y como explica el profesor del CNIM-CSIC, el acero verde surge de la necesidad de la industria siderúrgica de conseguir métodos de producción capaces de reducir su huella de carbono. La solución más interesante pasa por el empleo del hidrógeno en el proceso de reducción del mineral de hierro.
Actualmente, se producen unos 2.000 millones de toneladas de acero a nivel mundial, lo que equivale a unos 250 kilogramos por persona al año. Y, de acuerdo con el World Economic Forum, esta producción está detrás del 7% de las emisiones de gases de efecto invernadero (GEI). El motivo por el que la industria siderúrgica es tan intensiva en carbono está en los procesos de extracción de hierro y en la utilización de altos hornos que alcanzan temperaturas superiores a los 1.000 oC. Estos procesos consumen mucha energía, por lo que hasta ahora han dependido casi por completo de los combustibles fósiles.
El profesor del CNIM-CISC aporta cifras para entender la magnitud del problema: por cada tonelada de acero producido en 2022 se emitieron 1,9 de toneladas de dióxido de carbono (CO2), lo que equivale a más de 3.500 millones de toneladas anuales en total. “Si a esto sumamos que, como ha señalado recientemente la Agencia Internacional de la Energía, las emisiones mundiales de CO2 están aumentando significativamente hasta alcanzar un nuevo récord de 37.400 millones de toneladas en 2023, podremos deducir fácilmente la gravísima amenaza a la que nos enfrentamos”, explica De Damborenea.
La ruta hacia el acero verde
De acuerdo con el profesor del CNIM-CISC, el camino para descarbonizar el sector del acero y mitigar así el calentamiento global es complicado, pero no imposible. Tal y como explica, utilizar hidrógeno verde en lugar de quemar coque y mineral de hierro –como sucede en los procesos para producir acero convencional–, puede suponer una reducción del 90 % de las emisiones de CO2 emitidas por la industria siderúrgica.
“Los estudios realizados en la actualidad ya muestran la posibilidad de producir hornos de plasma de hidrógeno con una reducción de emisiones de CO2 de entre el 80 y el 100%. El proceso permite la fusión y la reducción de óxidos y chatarras simultáneamente en una única operación”, explica Damborenea.
Las principales dificultades son conseguir que todos los sectores implicados (industria, gobiernos e investigadores) trabajen de manera conjunta en el desarrollo y la implementación de soluciones; aumentar la capacidad de producción, distribución y almacenamiento del hidrógeno verde en grandes cantidades; y reducir el precio de producción del hidrógeno con energías renovables.
“En estos momentos, el precio de la producción de hidrógeno mediante tecnologías limpias como la eólica o la solar ha caído ya un 60%, lo que abre un camino prometedor. Pero la industria, para ser competitiva, necesita bajar el precio del hidrógeno de 10 euros por kilo a 3 euros. La Unión Europea calcula que puede llegarse, incluso, a precios inferiores a 1,8 euros por kilo en 2030”, señala de Damborenea.
Otro gran reto, en palabras del profesor, es que las políticas medioambientales que se están planteando tanto a nivel europeo como mundial no sufran un retroceso que nos devuelva a la casilla de salida.
La importancia del ecosistema ‘cleantech’ en la descarbonización del sector del acero
Aunque su implementación es más lenta de lo esperado, el acero verde va ganando impulso a nivel global gracias a diferentes iniciativas y proyectos del ecosistema ‘cleantech’ que tienen como principal objetivo reducir las emisiones de CO2. Grandes siderurgias, como ArcelorMittal, SSAB, Tata Steel, Salzgitter, Voestalpine o Thyssenkrupp están construyendo demostradores y plantas piloto y de producción en Europa.
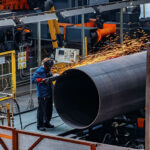
En EE. UU. destacan nombres como US Steel o Electra, y en el continente asiático lo hacen otras empresas como la coreana POSCO o las chinas Nippon Steel Corporation o China Baowu. “Brasil, con una planta de producción, y Chile, con una planta piloto, también se han comprometido con el desarrollo del acero verde. Y, de entre todos los países comprometidos con este cambio, debería resaltarse el papel de Suecia con proyectos como HYBRIT o H2 Green Steel”, explica De Damborenea.
En España destacan proyectos como el de Hydnum Steel. De acuerdo con el informe ‘¡Hablemos del acero!’, de Ecologistas en Acción, esta fábrica ubicada en Puertollano y apoyada por Siemens se prevé como la primera productora de acero verde en la península ibérica. “Aspira a convertirse en la primera acería verde de España y una de las primeras de Europa. El plan inicial es comenzar con una producción de 1,5 millones de toneladas de acero laminado empleando hidrógeno verde para la reducción de hierro. Pero lo más novedoso de la propuesta es que todo el proceso, desde la producción de hidrógeno hasta la propia elaboración del acero, se hará mediante el empleo de energías renovables. Todo un reto, no carente de riesgo, en innovación y desarrollo de producto”, señala el profesor de investigación del CNIM-CISC.