What is a digital twin and what is it for?
The virtual replica of a real product, service or system can help anticipate potential issues and curb risks by testing new functionalities before rolling them out.
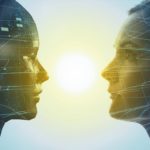
According to a number of consulting firms, in recent years, the modeling of digital twins has crystallized to become one of the most promising technological trends. But what exactly is a digital twin? Broadly speaking, a digital twin is a virtual rendering of a product, service or process, which is capable of simulating the behavior of its physical counterpart, whose reactions under specific scenarios can be monitored and analyzed to improve its performance and efficiency.
By replicating the structure and the information handled by the actual object, the digital twin can be used for running risk-free virtual trials and tests, a feature that is particularly beneficial in manufacturing processes. In fact, Gartner predicts that by 2021, half of large industrial companies will use digital twins, resulting in those organizations gaining a 10% improvement in effectiveness.
Michael Grieves, a computer engineer at University of Michigan first introduced the use of the term digital twin in the Industry 4.0 in 2003, at his Executive Course on Product Lifecycle Management. The term, though, was coined in the 1980s by NASA engineers. During that decade, the US space agency began using virtual simulations to predict the behavior of space shuttles or equipment, with the aim of ensuring the viability of certain missions and the physical integrity of astronauts. Today, as technologies such as big data, cloud computing, and the internet of things (IoT), reach critical mass and become more easily available, an increasing number of organizations and sectors are being able to start modeling their own product’s digital twins.
Main benefits
Merging the physical and virtual worlds, digital twins enable the performance of in-depth information analyses, based on which - and leveraging big data, IoT and AI solutions - it is now possible to thoroughly control systems to detect and remedy potential issues, prevent Downtime, test new business opportunities, plan future scenarios through simulations and customize production based on customer requirements.
By having a virtual replica, it is now possible to immediately gather 'feedback' about the activity in progress and apply eventual corrective measures in record time. For this reason, digital twins are particularly useful for the maintenance of connected machines and equipment units that generate and analyze large volumes of data.
How do they work?
To work with this technology, the first step is to develop solutions capable of collecting the information generated by the different components of the physical element. This requires fitting out sensors and other devices capable of collecting data on the status of the process, product or service in real time. In turn, these physical components must be connected to a cloud-based system, capable of receiving and processing all the information it gathers, in addition to comparing it against other contextual parameters. From there, it is already possible to virtually replicate the process, product or service and tweak it to try out any changes, which will only be applied physically once their success in the digital environment has been proven.
In order to facilitate the implementation of a digital twin, Gartner has singled out the four pillars that will help companies overcome some of the challenges posed by this type of projects:
- Establish standardized approaches to modeling
- Involve the entire product value chain
- Ensure access to multiple sources for data collection
- Ensure long-term access to models and their evolution
Once a virtual representation is rendered, it allows expediting innovation processes inside the organization, following a model that keeps gaining traction in the age of the Industry 4.0.