Software Designs Products by Simulating Evolution
Autodesk developed the computer-aided design software, called Dreamcatcher, over the past seven years. Among several approaches, it uses algorithms that mimic the process of evolution to produce new designs after starting with a list of parameters chosen by the user.
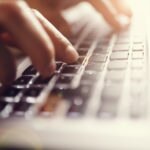
Software that can “evolve” novel component designs could help designers and engineers by automating part of the creative process.
Autodesk developed the computer-aided design software, called Dreamcatcher, over the past seven years. The California-based company already makes 3-D software that’s widely used in architecture, engineering, animation, and other industries. But Dreamcatcher takes a novel approach known as “generative design.” Among several approaches, it uses algorithms that mimic the process of evolution to produce new designs after starting with a list of parameters chosen by the user.
Dreamcatcher shows how even creative industries could be changed by automation (see “How Technology Is Destroying Jobs”). “Designers worry it will take their job away, and [they] doubt that it can create beauty”, acknowledges Autodesk’s senior director of design research, Mark Davis.
Dreamcatcher’s simulated evolution process begins with the software offering a set of potential solutions to a problem posed by the user. The software then “breeds” a new generation of solutions by recombining the best of those designs, as chosen by the user, and adding some random variation. The software can repeat this process to produce thousands of designs (see “Unnatural Selection”).
When a product designer or engineer feeds design goals—along with parameters such as materials, performance criteria, and cost constraints—into Dreamcatcher, the results may look nothing like conventional designs. Asked to create a chair, for instance, Dreamcatcher may produce legs made of a confluence of interwoven scaffolding rather than the usual solid ones.
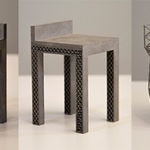
Three chair designs produced by the Autodesk software. - MIT Technology Review
“Generative design software has been mostly on the fringe for 30 years,” says Hod Lipson, an expert in 3-D fabrication at Cornell University. “Hollywood animators, gaming developers, and computer artists made beautiful, elaborate effects with it,” he says, adding that it is likely to become more common because it complements the flexibility offered by 3-D printing.
Designers at Autodesk used Dreamcatcher to design a unique carbon fiber swingarm—a component that provides rear suspension—for a super-fast electric motorcycle, the LS-218, made by Lightning Motorcycles of San Carlos, California.
Dreamcatcher was fed files of a normal swingarm that had been produced by earlier versions of CAD software. The designers also fed in the width of the tire with clearances, the forces that would come with the weight of a rider, the available materials, the forces from wind and gravity, and size limits. Dreamcatcher kicked out a design for a swingarm made of hollow intersecting triangles sheathed in carbon fiber.
“You can make things that are structurally stronger from an engineering perspective” using generative design, says John Maeda, a prominent designer and a partner at the venture capital firm Kleiner Perkins Caufield & Byers. “Generative design is an exuberant field of discovery with many good things coming out of it.”
Lightning Motorcycles expects the swing arm to improve the LS-218’s acceleration, performance on curves, and predictability. If it performs well in road tests and races, bikes with the carbon fiber swingarm will be shipped next year.
Dreamcatcher has so far been used to make just a few other functional components including a bracket for a spacecraft and a bike frame. But Autodesk hopes that industries from architecture to construction will adopt the generative software when it’s commercialized.